Podcast | Technology & Business Solutions (TABS)
Beyond the Chips: How Automation Supercharges Semiconductor Production
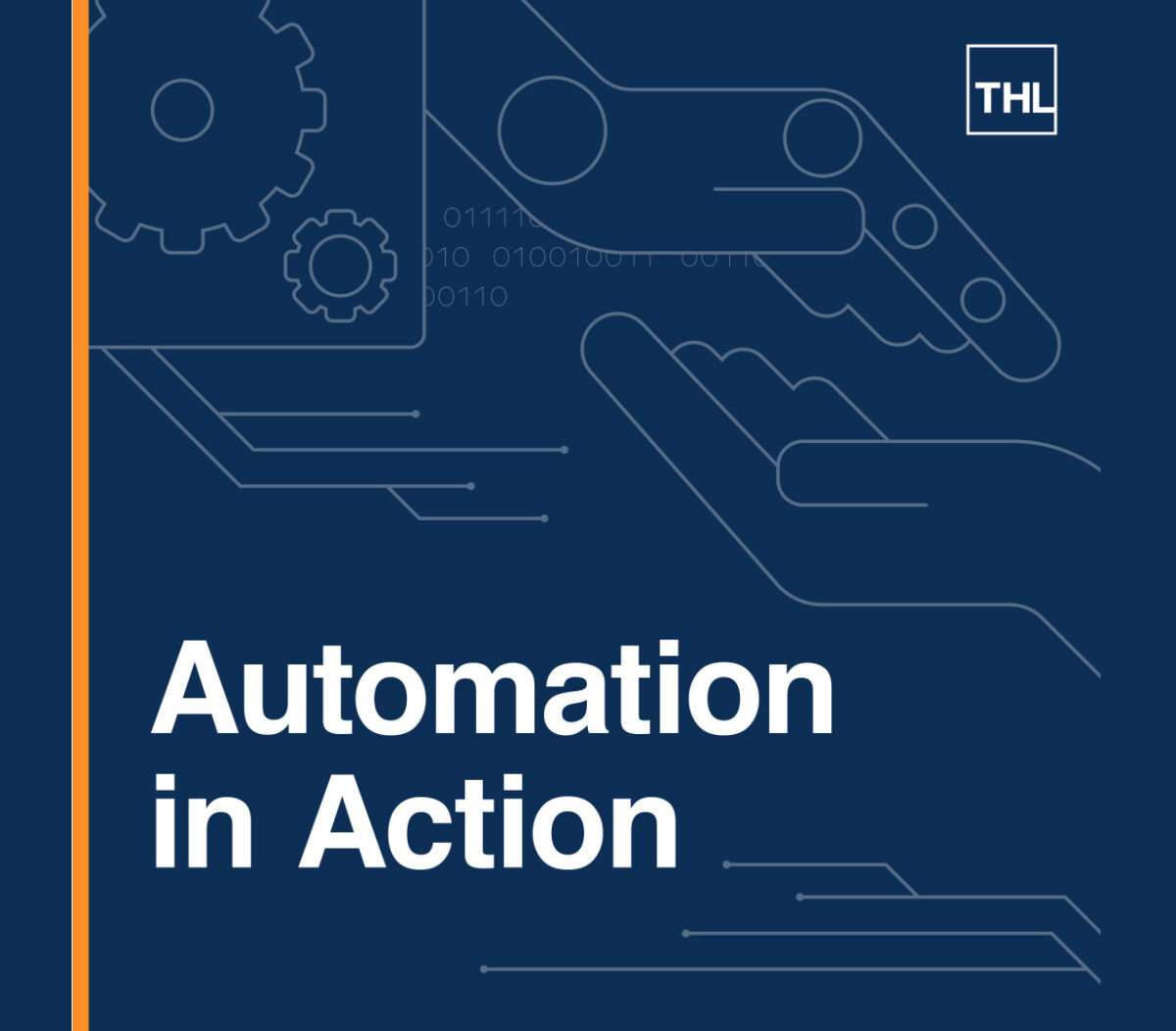
THL’s Automation in Action, Episode 3
Semiconductors are a backbone of our national economy. From government defense systems to our smart phones and computers, we rely on them in ways most of us rarely pause to consider. That’s why the Biden administration and Congress have made it a top priority to boost the domestic manufacture of semiconductors.
But semiconductors are notoriously complicated and expensive to produce. In this episode, we speak with Dave Jarzynka, CEO of Brooks Automation, a leading provider of precision robots that serve the global manufacturing of semiconductors. We’ll learn about the complexities and costs of manufacturing semiconductors, and how automation plays a key role in facilitating their production.
Key takeaways from this episode:
- The scale of technologies semiconductors that enable, and why they are so important to the global economy.
- The nuances of semiconductor manufacturing, and the specialized environment of the Semiconductor Fabrication Plants (FABs) required for their production.
- How AI and other emerging technologies may impact semiconductor demand and manufacturing.
To learn more about THL’s cross-sector strategy to uncover opportunities in emerging technologies, visit THL.com/automation
Dave Jarzynka [00:00:04] The microprocessor on your smartphone has eight billion of these tiny switches in them, believe it or not, eight billion. And on a semiconductor wafer, they’ll make many of these devices. There may be a trillion. So all of these tiny little logical pieces are being put together and then used to produce a task for you. Yeah, you don’t see it because they’re so small, they’re low power and they’re working behind the scenes. But which you should know is without semiconductors, today’s cars aren’t working. Your smartphone doesn’t work. Your computer doesn’t work.
Jim Carlisle [00:00:36] That’s Dave Jarzynka, CEO of Brooks Automation, a leading provider of precision robotics that serve the global manufacturing industry around semiconductors. And I’m Jim Carlisle, and this is Automation in Action, where we pull back the curtain on automation technology and lead you on a journey inside. I’m here with my colleague Sarika Ramakrishnan, who had the chance to sit down with Dave and discuss semiconductors, the backbone of our national economy. Interestingly, and according to the Semiconductor Industry Association, last year, U.S. exports of semiconductors totaled 61 billion dollars, and we’re the nation’s fifth largest export sector, behind refined and crude oil, aerospace and natural gas. The association also estimates that the sector currently accounts for 370,000 direct jobs and another 1.7 million jobs indirectly. All of those numbers actually seem small to me. It’s really hard to exaggerate the importance and reach of the semiconductor industry. In this episode, Sarika and Dave discussed the complexities and costs of manufacturing semiconductors. Sarika, what was your biggest takeaway from your conversation with Dave?
Sarika Ramakrishnan [00:01:52] Most people know that semiconductors are critical to modern technology. They’re what makes smartphones and airplanes work. We need them for a power grid for NASA’s moon mission, for military applications. A calculator that you’d use in math class might need a single chip, but new electric vehicles often require thousands. They’re a critical part of the supply chain, a key component of the global economy and even a matter of national security. That’s why President Biden in Congress passed the CHIPS Act in 2022, which allocated 50 billion dollars over five years to bolster domestic production. But they’re also very expensive to manufacture and very complicated. I didn’t appreciate just how much until Dave really placed it in perspective.
Jim Carlisle [00:02:40] Definitely. You know, as our investment team became more interested in semiconductors and automation around that, we learned a lot about the manufacturing process for semiconductors. The construction of semiconductor fabrication plants or fabs, as they’re called in the industry, are extraordinarily complicated and incredibly capital intensive. Semiconductor manufacturers have already automated huge parts of their process, and it’s really about the improvement of those robotic systems, of those automation technologies that the industry is pushing forward today. That’s why we have such tiny chips that fuel everything that we do around electronics and cell phones and airplanes, as Sarika illustrated before. So anyway, Dave’s the best expert on this. Should we hear more from Dave?
Sarika Ramakrishnan [00:03:29] Let’s get into it. Could you tell us briefly about your career, your current work and how you came to be involved in the semiconductor space?
Dave Jarzynka [00:03:45] I started in a semiconductor business about 36 years ago. Back then, semiconductor fabs were really not automated, mostly manual. We put move things around, so I had the privilege of working with some of the first robots at the beginning of automation in semiconductors.
Sarika Ramakrishnan [00:04:01] Could you tell me a little bit more about Brooks, the genesis of Brooks Automation’s technology and how the company has evolved over time?
Dave Jarzynka [00:04:09] Early on, the company started as not a generic automation company. There was very little automation back in 1978 when the company started. All of automation space was new. Its initial mission was to automate semiconductor fabs. That was a growing need. So it started out as a very small company and became the standard for automation and memory semiconductor fabs. In fact, today, just about every semiconductor on the planet Brook has touched. So what does that mean to you? Any electronic device that you have, whether it’s in a hospital, in a car or in your house, you name it. Brooks Automation has probably touch that semiconductor. That’s how prevalent we are in today’s semiconductor fabs. That’s how much they rely on us. We took that hard. We have a purpose that’s very meaningful. The good news is the challenges continue to get greater as these applications advanced and they need more of our stuff. So we see that continuing for a very long time.
Sarika Ramakrishnan [00:05:06] Before we jump in, let me ask a fairly basic question. I imagine the answer is likely a little more complicated. What is a semiconductor?
Dave Jarzynka [00:05:15] Big question. It’s a popular word, but a lot of people probably haven’t touched one or seen one. I’ll give you a very simple explanation. Start with a light switch. Think of something that goes on and off at it’s basic principle, right? And when you shut it off there, a light bulb does a light. And when you turn it on, it does. And so that’s what’s called logic on or off. And so what happens in a semiconductor is it takes all of these logic sequences and produces a task. It allows it to get a result. And the way you do that is you build a structure with different materials called a transistor that is basically a switch that you can control with precision. The difference here is a light switch is pretty big. The microprocessor on your smart phone has eight billion of these tiny switches in them, believe it or not. And on a semiconductor wafer, they’ll make many of these devices. There may be a trillion. So all of these tiny little logical pieces are being put together and then used to produce a task for you that kind of take advantage of every day, you don’t see it. Because they’re so small, they’re low power and they’re working behind the scenes. But what you should know is without semiconductor, today’s cars aren’t working. Your smartphone doesn’t work. Your computer doesn’t work. Some of the most sophisticated medical equipment in the world don’t work. If you think about the mineralization of many things, people that are now able to have medical devices that are portable across the board. There’s a lot of life saving things that are now enabled because semiconductors are so small and so powerful everywhere around us. They’re truly have a different purpose. They’re also enabling us to have fun, right? Video games and enabling virtual reality and everything that we do today. The key to this is that you have to think about is as these problems get harder, you just need more logic. And the way to get more logic is to invest in the technology in semiconductors and make things smaller and more powerful. And when you make them more smaller and powerful, you got to rely on more automation because it’s harder and you need to rely on that automation to be very predictable and do the job.
Sarika Ramakrishnan [00:07:17] The scale is mind boggling, but maybe tell me a little bit more about the complexity in manufacturing of semiconductor.
Dave Jarzynka [00:07:25] It’s really important what a semiconductor wafer is. It’s a thin substrate made of silicon. It’s about a foot in diameter. Important point here is semiconductors are made on this maybe a thousand different steps. The feature sizes are at atomic levels. So there is about a thousand pieces of equipment that are located in a manufacturing facility, a thousand times cleaner than an operating room. Earthquake proof. Gases that are toxic, so rare, a lot of different materials coming in here, this complicated process. And contamination is really the enemy. Any time anything of any size gets on this wafer, it can cause the device not to work. So you lose money. So the challenge is what do you do in this manufacturing environment to be able to get what they would call very high yield, very high success in these devices. So they move this equipment into the fabrication facility. And what they rely on is automation. It’s today’s fabs are pretty much lights up. You won’t hear a lot. You’ll see a lot of equipment connected to each other and inside a lot of the equipment we have Brooks Automation products. Moving these highly valued substrates being processed in tools. And then these will be put into carriers that move these around from tool to tool, and Brooks makes sure those carriers are clean. So we touch this wafer throughout the entire process of a semiconductor fab as it moves through it. Fabs are open 365 days a year, 24 hours a day, seven days a week. Our automation runs seven or eight years nonstop without failure.
Sarika Ramakrishnan [00:09:04] I’d be curious if in that level of detail you could also outline the increased complexity within a fab that was built, let’s say five years ago versus a fab built today.
Dave Jarzynka [00:09:17] Typically when they make a new factory, things are getting smaller. The devices, the features are getting smaller, and at this level you’re going from 50 atoms to 20 atoms, so very small. And when things are small, they’re fragile. They’re exposed to not work, right, if they get contaminated at the lowest levels. And what small means to them is couple of things. They can put more of their devices on a wafer, which makes the economics better. And usually you can also increase performance. You increase performance and you lower costs. The only way to do small is to make sure that the process is extraordinarily repeatable with low variation. The best way to do that is with automations. That’s one key piece. The second is also on cost. If in a factory you have, let’s say, 20 of the same tool running the same process, in the next factory, they want to understand how they can reduce that cost. And so the trend is to put more of these process. They call them modules within a smaller area or cluster them around a circle. Key to doing that is a different automation system that can do this in a cost effective way, right? So instead of moving away four to six stations, let’s see if we can move it to 12 stations and save money. Right? So that more steps are happening with the same amount of space. So again, that requires retooling the automation set. The third vector is the processes themselves create contamination. Not just materials, but even gases. And so we’re specialized in our contamination control business so we’re moving those. So we’re also helping the next gen semiconductor fabs by coming up with new ways to detect and remove these materials that are on the carriers that could end up damaging wafer and causing yield. All three of those are a super megatrends in a fab that are extraordinarily important for making the economics of fabs work in the future.
Jim Carlisle [00:11:18] From the top of your discussion, it’s clear that demand has exploded over the past decade. The global market for semiconductors has increased by three and a half times to 570 billion dollars, and it shows no sign of slowing. It’s an area of increased investment. Last year alone, there were 180 billion dollars in new capital investments. A lot of that capital is also going into the United States. It’s a really exciting time to be investing in this space.
Sarika Ramakrishnan [00:11:47] That’s right. Demand for chips is on the rise, but so is demand for increased sophistication, better performing chips, but also better performing fabs, which of course, is where automation comes in.
Jim Carlisle [00:11:59] Let’s hear more about that.
Sarika Ramakrishnan [00:12:05] Given your background and experience in this space, could you maybe walk us through what automation means in the semiconductor landscape and how that’s evolved over the last few decades?
Dave Jarzynka [00:12:19] It’s a really good question because it’s quite a story of the benefits it provided. It’s a very very small and they’re doing it at very, very large volume with sophisticated equipment. So as you can imagine, back in the day, people would move these by hand. What would happen is you get a lot of defects. People make mistakes and contamination gets in the way. And then when you get defects, none of those chips are good. So the challenge they had was how do you lower the cost of manufacturing these things while advancing the technology? The path they chose was automation, which said of people, you have robotics and automation solutions that pick these things up and move them throughout the fab and the tools. And today, if you went into a semiconductor fab, all of it is automated. There’s very few people. So it’s gone from, you know, just 1987, the beginning of it in a short period of time. It’s completely automated, which is to reduce the cost of semiconductors by thousands of times and allowed semiconductors to be ubiquitous across the globe.
Sarika Ramakrishnan [00:13:18] That’s really interesting, especially given the context of this podcast and all of the guests that we’re speaking to across a number of different industries. I’d say semiconductor space is probably the most automated and has one of the highest levels of automation penetration and would love to get your perspective on the dynamics of the industry that have fueled and supported that love of automation penetration.
Dave Jarzynka [00:13:45] Everything you touch today probably has a semiconductor in it. In your daily life, think about what have smartphones have done for you and and life-saving equipment and GPS systems and everything around you has semiconductors. And the reason that’s enabled is because the cost of semiconductors, the performance of them has gone up quite a bit. You may heard stories that we are at the beginning, computers taking up rooms, right. Now, you have a computer on your watch so you need to make them smaller, more powerful and cost effective. And there’s a lot of technology that went into developing that, but one of the core foundations is doing it highly automated. So what automation does for them is it provides very little variation in everything they do, so they’re able to very predictably manufacture these in high volume with very low contamination and very few mistakes. If the investment has not slowed down, there’s a lot more problems to solve and automation is at the forefront of science.
Sarika Ramakrishnan [00:14:45] What parts of the semiconductor manufacturing process, would you say, is most ripe for further innovation from an automation perspective?
Dave Jarzynka [00:14:55] Yeah, two pieces. There are very many different types of processes when you manufacture a semiconductor, and a handful of those are processes that cannot be exposed to oxygen. So they’re in a vacuum, like being in space, which means you have to put automation in the area where not only can you not have contamination, but some of the dynamics change when you don’t have air available. So we provide highly specialized automation that works in these vacuum tools. Some of these tools cost 5, 10 million, 20 million dollars. They rely on our vacuum automation solutions to handle that very valuable wafer. Sometimes that wafer is worth a million dollars and we move it around their tools. So that’s one area. The second area is a word I said prior, which is contamination. And contamination in this world is things you usually can’t see. It’s so tiny. And the fact is when you make a wafer, there are so many materials and things that are used. The carriers that these wafers go in throughout the fab get very contaminated. And so we purify [00:15:59]there and [0.1s] we see a lot of growth there just beginning early innings. So that’s an example where we’re not only automating with robotics or taking a high value problem, mapping it all out and automating it from top to bottom, the handling the software, the process flow and adding value to a fab to help them avoid mistakes and help them save money and be more efficient.
Sarika Ramakrishnan [00:16:20] What are some of the complications involved in semiconductor production from a cost, logistics and precision standpoint?
Dave Jarzynka [00:16:30] Yeah. So from a cost point of view, I describe the word yield. Whenever you make something, the question is how successful were you? If you made 10, can you ship 10 and have people pay you for 10, or do some of those have defects? And when you’re thinking about semiconductors, it’s very sophisticated technology, very difficult technology. The key to making money is one of these semiconductor fabs cost about 15 billion dollars to put on line. You need very high yields, which means you need very low defects, which means you need very low variation. And that’s what automation really provides, is that foundation or sure, across the board, that’s one piece of it. Secondly, speed is extremely important. Being able to move fast, be very lean in a production environment. So being able to produce a lot of product in a very small area very quickly and automation does a much better job of that than manual steps. So it’s allowed semiconductor fabs to redefine workflow to work differently in a way that’s much more efficient, much more scalable and a lot less space. Therefore, they can put more things in the fab, make more product and get a higher return on that now.
Sarika Ramakrishnan [00:17:43] What are you looking forward to from an automation perspective as you think about the new semiconductor innovation that’s coming online?
Dave Jarzynka [00:17:51] We’ve been flagging and tracking different applications for many years. You know, one of the latest was 5G technology, and that drove a lot of semiconductors, autonomous vehicles. And we started talking about A.I. artificial intelligence. And we’re just seeing the signs of AI becoming real from a semiconductor point of view. AI needs a tremendous lot of computation power, tremendous amount of memory subsystems. To be successful, to actually work in real time. So it simply drives drive silicon demand very high. The piece we really like about it is it drives the most advanced type of silicon. So this requires large capital investment and brand new semiconductor facilities with new tools that require all new automation. So what you’ll see with A.I. or you’ll see new semiconductor fabs being built and Brooks is engaged today and many new opportunities for tool architectures to automate them and tools for contamination control that can meet those specifications. We see a very large opportunity as A.I. grows for us to grow with it, and that’s to create more value in the market. It’s exciting space.
Sarika Ramakrishnan [00:19:02] Can you explain in layman’s terms how companies like Brooks are helping to meet this rising demand and bring new efficiencies to production?
Dave Jarzynka [00:19:14] I’ll give you a real example that you can relate to. Many of you may have an iPhone. It’s a well-known fact publicly that inside the iPhone, Apple’s microprocessor is made by a company in Taiwan called TSMC. So they manufacture the process for the iPhone. Brooks was involved in that when TSMC in Taiwan is going to put a new factory online to meet the needs of Apple, they are mapping out the toolsets that they need to do that. And so what Brooks will do maybe 18, 24 months before this factory is real is will work with many equipment manufacturers on new automation sets and then will work directly with the fab on our contamination control technology. So first of all, we have to solve the problems that they have, and we’re very good at that. We have a lot of types of people to do that. But secondly, it must be on time. You can imagine if they’re going to launch a new iPhone, this product needs to be ready. So you need to be very good and predictable at delivering advanced technology. We’ve proven we’re exceptional. You can really count on Brooks. We like to say right the first time, every time. And that’s a big piece of our value. We deliver and solve really hard problems on time. And that ends up being in the factory, enabling these manufacturing lines to run like they need to.
Sarika Ramakrishnan [00:20:30] You’ve mentioned a lot about the kind of secular tailwinds that are driving increased volume, demand for semiconductors and greater complexity and increased needs for [00:20:43]CapEx [0.0s] and production infrastructure. Could you explain what exactly is involved in getting a semiconductor fab online and instituting a new production facility? Kind of a broad question, but would be helpful to understand all of the component pieces and how the automation actually is instituted from the beginning.
Dave Jarzynka [00:21:08] So first of all, keep in framework a factoring may cost 15 billion dollars, right, and many times they’re building a new building. These buildings are earthquake proof. These buildings have clean rooms that are 10,000 times cleaner than an operating room, very sophisticated. They use a tremendous amount of exotic chemicals and materials. There’s a lot of things going on in the semiconductor fab. And to operate, you need to move in about a thousand pieces of equipment. They may cost anywhere from 3 million to 150 million tool. Very expensive equipment that takes a lot of R&D to put in line. To give you an idea two years before that starts, Brooks will get designed into a lot of this equipment and then finally it starts to get moved in to these semiconductor fabs. The great news is once they prove that equipment in the line will then add more production capacity. And because Brooks was a very strategic partner to either the fab or these manufacturers and qualified, we ramp with it. It’s very intensive process for an extension of our customers. So it has a lot of stickiness, right, once your solution is qualified. Good news is we can see what the future looks like a little bit before it happens. We know what our business will look like in a couple of years. And if that capital spending remains in place and secular winds turn into more factories, which that is the trend, we can see where our automation is going to go so it gets installed. To give you an idea, those factories may run for 20 years without equipment. And so we get an annuity of also maintaining and servicing that equipment. But what’s really exciting is even though that technology was advanced in 12 to 18 months, they need new technology. Semiconductors need to be better, so they build new factories. And the demand for silicon fact is expected to grow from 500 billion this year to over trilion dollars by the end of the decade. So the need for more factories is there. So once you get qualified, once you build, the process starts over and it really shows growth.
Sarika Ramakrishnan [00:23:04] The semiconductor industry is in the midst of a lot of geopolitical tension and debate and wanted to better understand how you manage that risk and also whether you see it as an opportunity or as a headwind, particularly as you’re looking to help fuel automation of the semiconductor space.
Dave Jarzynka [00:23:27] Really good question. So first of all, we have to pay attention to geopolitical risks, right. At the scale of capital invested here, there is real things that can impact that. So we put a lot of attention into it. When we look at some of the regional dynamics, one of the very positive drivers is semiconductors are becoming more strategic than oil. Consumers are realizing maybe you can’t buy the car you want or get the device you want, or in some instances that’s even scarier. Maybe there’s not medical equipment available. The industry went through a shortage. And so what’s happened there is not only are semiconductor fabs responding to that, but governments have started to realize, well, if I can’t get semiconductors for the things that I want to do as a government, what does that mean to us? That has really sprung out to creating a lot of funding for semiconductor fabs in different areas of the world. So that’s spurred even more investment in having leading edge and semiconductor capability in every region more that even more to today. The good news is if there’s things that get worse in the world, if one region is difficult for us, semiconductors need to happen and another region will grow. For example, if China was ever pulled back on investments or Korea was pulled back and North America is investing current heavily with the CHIPS Act, and that’s a win.
Jim Carlisle [00:24:51] Sarika, Dave is so articulate about the benefits of automation, in particular in the semiconductor industry, which is so highly automated and precise. And it’s an interesting case study versus some of the other end markets where we’ve talked about automation, like agriculture, for example, where it’s a much different environment as we’ve talked about.
Sarika Ramakrishnan [00:25:13] Yeah, totally agreed. And I think it’s a really impressive timeline in the semiconductor industry that went from zero percent automation in the 1980s where manufacturing was almost completely manual with people moving things around to today where there’s basically 100 percent automation and fabs are pretty much lights out. And I think it’s interesting to reflect on the market and process engineering dynamics that created that perfect storm enabling automation.
Jim Carlisle [00:25:48] Yeah, it’s it reminds me a lot of an article I read recently about the Jevons Paradox. You ever heard of the Jevons Paradox?
Sarika Ramakrishnan [00:25:56] I have not heard of the Jevons Paradox.
Jim Carlisle [00:25:59] So there’s this guy, William Stanley Jevons, as I understand it, who in 1865 wrote this seminal article about the consumption of coal in Great Britain. But his central thesis was that as steam engines became much, much more efficient, that more coal would be used. In Great Britain was a big coal producer, and people were concerned that as efficiency increased, as technology progressed, that the resource use would drop precipitously. And what they found, of course, and I think what we’ve seen time and time again, and the same is absolutely true in semiconductors, is that as one part of a process becomes more efficient because of technology, that new demand generators are unleashed. And I think it’s referred to now is the Jevons Paradox that as a part of the process, becomes more efficient. You don’t actually need less of that thing, you may need more of that thing because people have greater demand. It’s and I think the same has been true in semiconductors, where as that processes become so much more efficient and so precise as technology has been reduced, technology has improved, the end product has improved, semiconductors have improved. But wow, the number of jobs that have been created by the incremental demand that’s been unleashed by that technology.
Sarika Ramakrishnan [00:27:24] Yeah, I think that makes a lot of sense. And automation has really fueled a lot of that innovation, both in the semiconductor manufacturing process, which is then enabled innovation more broadly. I think to your point, it’s definitely a virtuous cycle. Automation and improved production efficiencies in semiconductor manufacturing has undoubtedly enabled further tech innovation, which results in more demand, which results in more innovation and so on.
Jim Carlisle [00:27:56] I’d like to extend a huge thanks to Dave for joining us on the show and to my co-host, Sarika Ramakrishnan. And thank you for listening to automation in action. Be sure to like and subscribe so you don’t miss an episode. Automation in Action is brought to you by THL. To learn more about THL cross-sector strategy, to uncover opportunities and emerging technologies, visit THL.com/automation.
- Verticals
- Technology & Business Solutions (TABS)
- ISO
- Industrial Technology & Software (incl. Robotics)
- Cross-Sector Strategy
- Automation
- Verticals
- Technology & Business Solutions (TABS)
- Cross-Sector Strategy
- Automation